The first blog on industrial flooring described various undesirable phenomena that affect the quality and durability of the work including cracking, curling, and delamination. The second part of the blog series focuses on the role of superplasticizers and why choosing the right solution is of such great importance.
A well-executed concrete floor is characterized by a smooth surface without any defects. However, a flawless end result can only be achieved if various complex measures are taken into account: from design to raw material sourcing and concrete mix formulation to execution. All steps must be precisely coordinated in order to achieve a high-quality result without compromising on time and cost efficiency.
The use of chemical admixtures is essential to achieve this. As explained in the previous blog article "Industrial Concrete Floors: Not an Easy Accomplishment”, a flooring system is always recommended that uses the most appropriate combination of different products, each specialized to solve a particular problem. This holistic approach can address the problems that can potentially arise during the construction of an industrial floor while maintaining control over the system and the progress of the work on the job site.
A high-performing flooring system typically comprises of the following products:
- Superplasticizers
- Shrinkage control agents
- Fibers
- Curing agents
In all concrete types and applications, the main purpose of the superplasticizer is to reduce the water-cement ratio to achieve the desired fluidity while retaining the expected mechanical properties at the same time. In the case of concrete floor applications, the choice of the correct superplasticizer becomes even more strategically important because several highly important criteria must be met that may not necessarily be of such relevance in other applications, namely:
The concrete mix must be very stable and not prone to segregation. Limited stability can cause bleeding on the surface or, even worse, separation, resulting in a non-homogeneous composition of the concrete throughout the entire depth of the floor and compromising the quality of the hardened concrete.
- The workability of concrete must be maintained for the entire time, from transport to pumping and placement. Concrete that has lost fluidity will become more difficult to pump and place, thereby increasing the time needed for the application and also increasing effort, manpower, and ultimately cost. Additionally, reduced fluidity has the potential to lower the degree of compaction and the quality of the structure itself. The retention of fluidity over time is particularly demanding in hot conditions.
- Finishing time is another important factor: there is an optimum time window for helicoptering operations. Concrete setting cannot be too fast, nor can it be too slow as both scenarios would be inadequate. If the concrete sets too fast, which can happen especially in hot climates, there is not enough time for proper finishing, where even accelerated operations can become a source of mistakes. On the other hand, if the hydration of the concrete is too slow, which occurs primarily in winter, helicopter finishing is often postponed leading to the floor not being completed on time and negatively affecting work schedules.
- The rheology of concrete is of key importance for ease of pumping, pouring, and laying. Reducing the workload and improving the workers’ experience will also contribute to the achievement of the best surface finish.
- The content and quality of air in the concrete must be completely under control. An excess of trapped air in concrete represents a source of surface defects and can reduce compressive strength.
For the above reasons, not every superplasticizer is suitable for the production of concrete floors. The choice of water reducer must be carefully considered under the guidance of experts. However, in summary, the optimal superplasticizer for concrete designed for floor applications should provide the following benefits:
- Optimal rheology for excellent pumpability and superior ease of laying
- Mix stability to avoid bleeding and/or segregation
- Facilitation of compaction and strike-off operations
- Reduction of surface finishing times, especially in winter
- Improvement of initial and final mechanical strengths
- Increased durability
Hot temperatures in summer and cold temperatures in winter present different challenges: in cold conditions, the concrete must be accelerated, while in hot conditions, workability must be maintained. Therefore, different superplasticizers must be used on a case-by-case basis.
Make sure to stay updated for our next blog post, which will focus on shrinkage and its impact on concrete floor quality and durability. We will provide detailed information on how to prevent or minimize shrinkage by implementing targeted measures during both the design and execution phases of concrete floor construction.
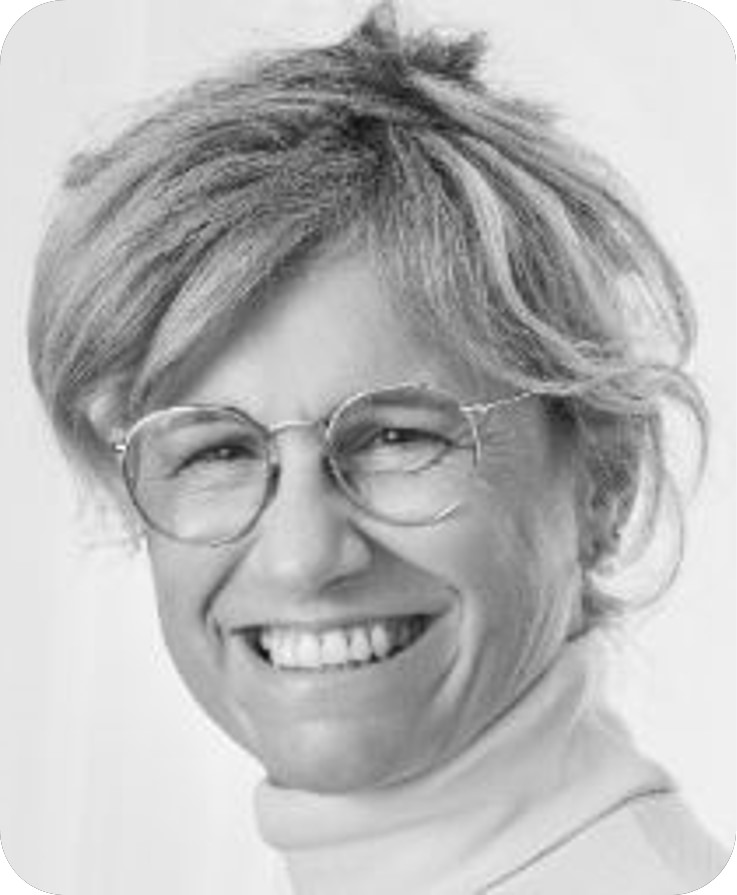
Nicoletta Zeminian