Today, screeds are based on two main technologies: the traditional dry cementitious screed and the anhydrite screed. Application of dry cementitious screeds is labor-intensive and time-consuming. Anhydrite screeds will be used less due to the increasing scarcity of raw materials. Master Builders Solutions has developed a new, innovative self-leveling screed (SLS) technology named Technology for SLS to set a new standard in screeds.
From a technical and economical point of view, cementitious self-leveling screed is a proven alternative to conventional technologies. Until now, attempts in establishing SLS as a regular screed technology have failed because shrinkage and the resulting curling were difficult to control, negatively affecting the quality and durability of the final finish of pavement for both wood and tile floor coverings.
Traditional dry screed
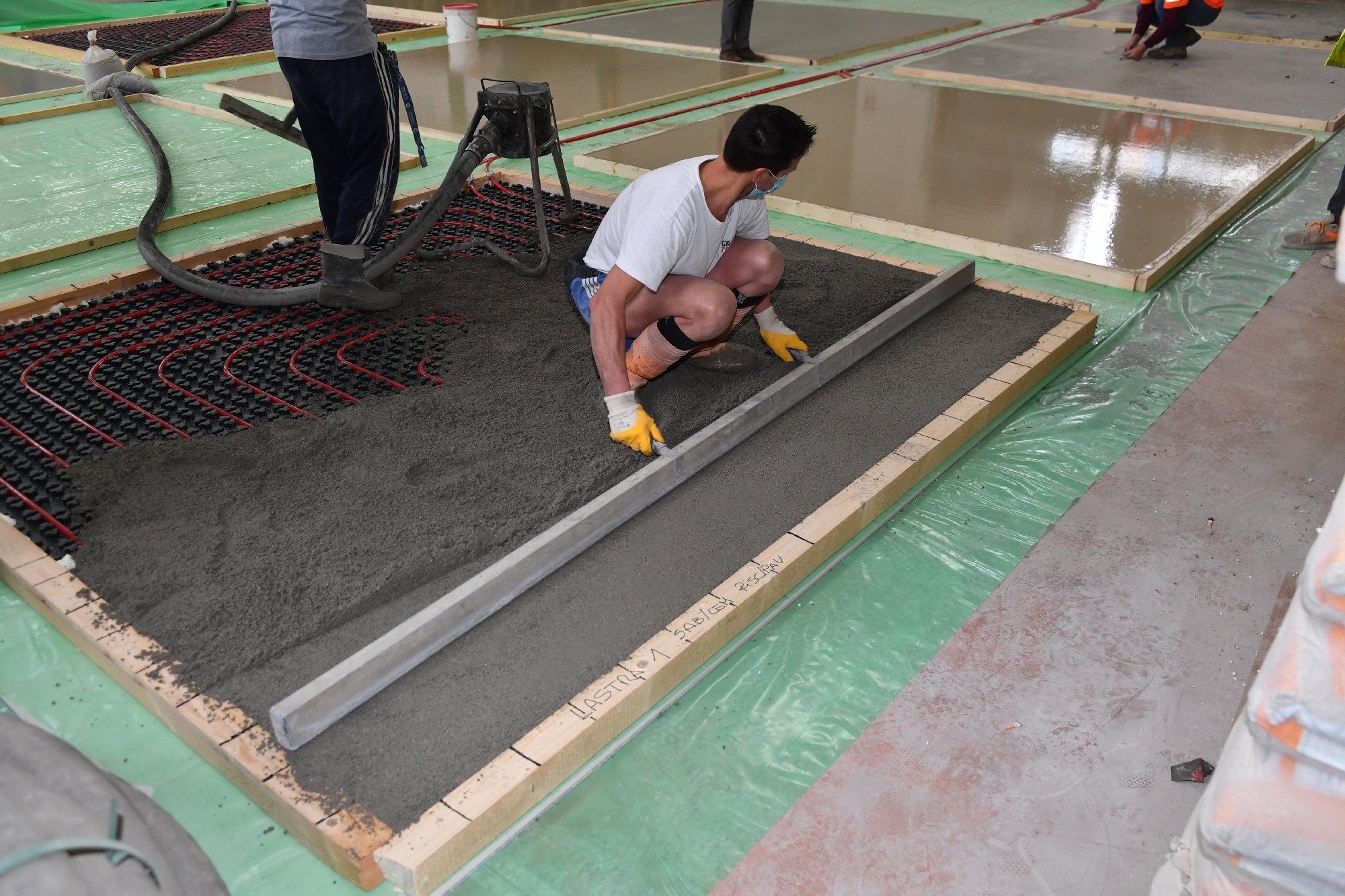
Self-levelling cementitious screed with Technology for SLS

Ahydrite screed
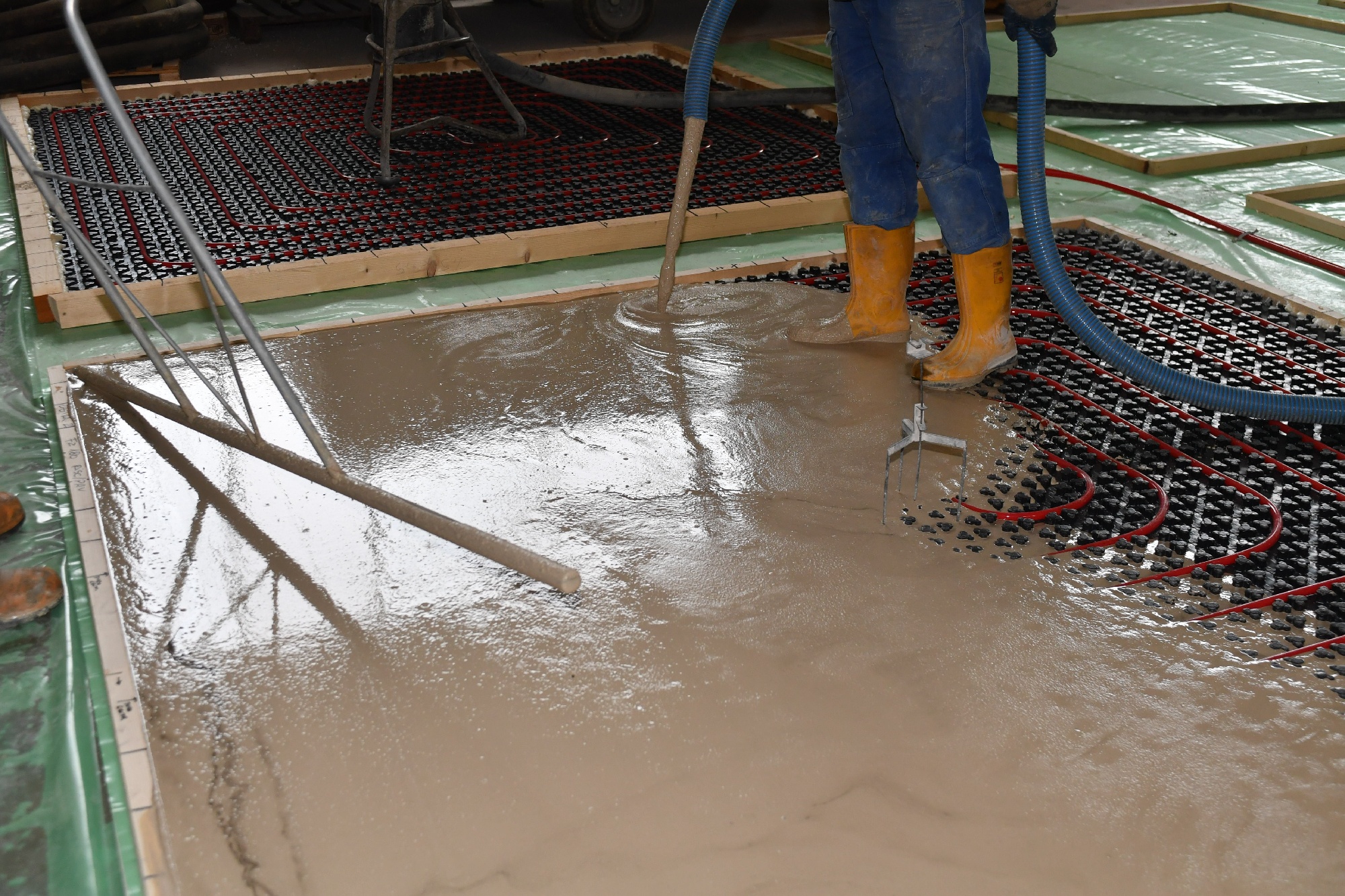
What is Technology for SLS?
The Technology for SLS is a unique admixture package for cementitious self-leveling screeds that enables easy processing for quick and economical installation. Stable and robust screeds can now be produced with highly controlled dimensional stability. Other benefits include:
- Construction times of up to 10 times faster
- Negligible shrinkage and curling
- Less labor intensive
- Applicators do not require special qualifications
- No need for additional polishing or curing agents
- Reduced construction costs
- Lower CO2 emissions of up to 20%
This new self-leveling screed technology can be supplied by a ready-mix manufacturer, directly by the applicator or can still be mixed on-site from silos.
A unique product package
The unique combination of a specific admixture package ensures optimal results for screeds in the fresh and hardened state, which includes:
- MasterLife SLS 200 forms the core of this technology and was specifically developed for self-leveling screed applications to control drying shrinkage and reduce the corresponding risk of cracking while counteracting curling.
- The latest generation of superplasticizers significantly improves concrete rheology and maintains the flowability of the concrete during transport and placement. A plastic viscosity reduction of up to 30% reduces pumping pressure and time.
- High-performance MasterFiber microfibers prevent cracking from plastic shrinkage while increasing concrete strength through their excellent bonding properties.
- MasterMatrix SCC 110 to prevent segregation in the fresh concrete mix.
- MasterKure curing compounds form a protective film over the fresh concrete to retain moisture and maximize the hydration potential of the cement for optimal strength development and durability to extend the service life of the floor.
Advantages that make the difference
A recent direct comparison* between the three screed technologies clearly showed the superiority of Technology for SLS over the alternatives in many categories. SLS is faster and by far easier!
Dry traditional screed: 15 min
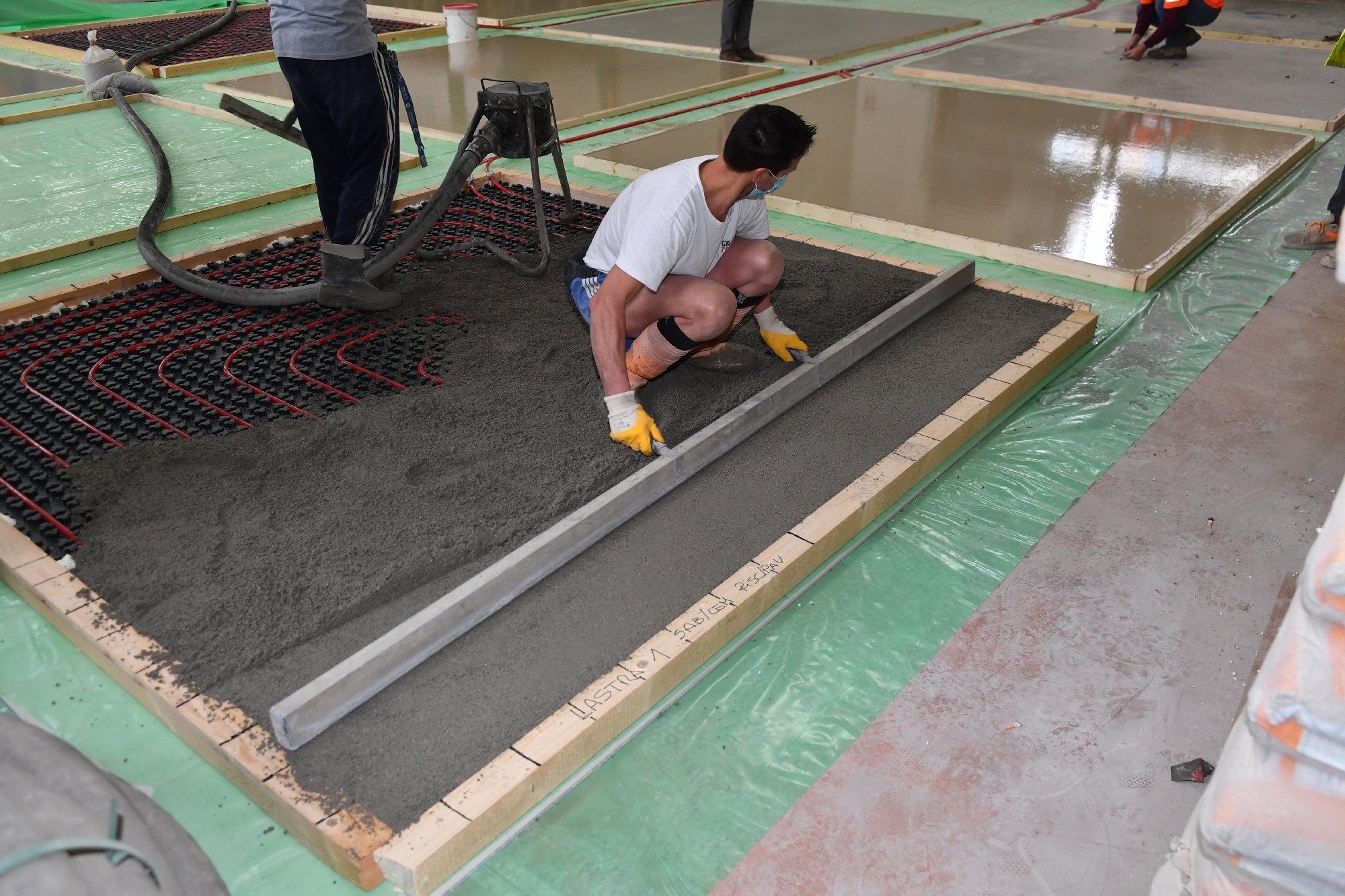
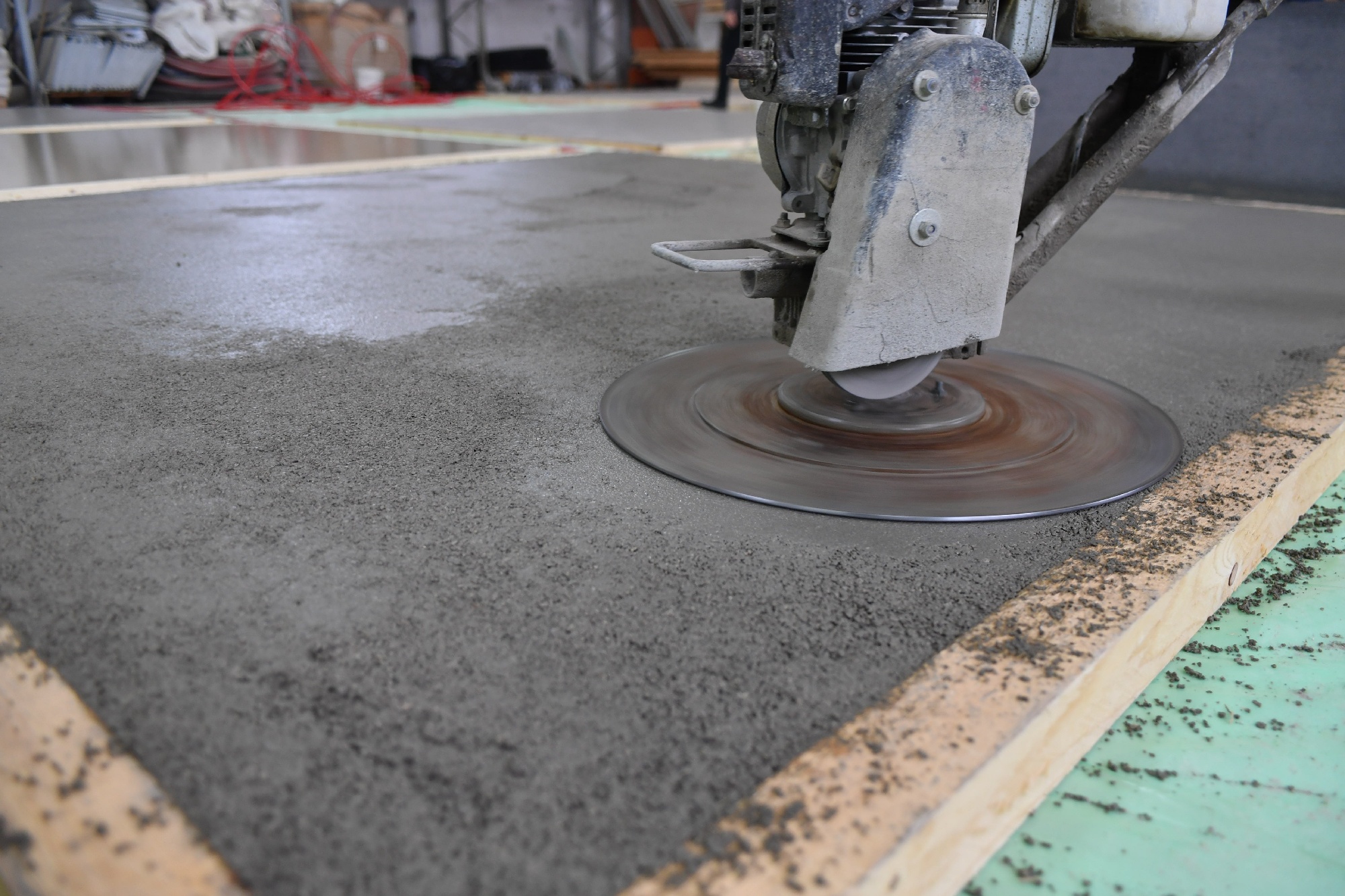
Technology SLS: 7 Min.
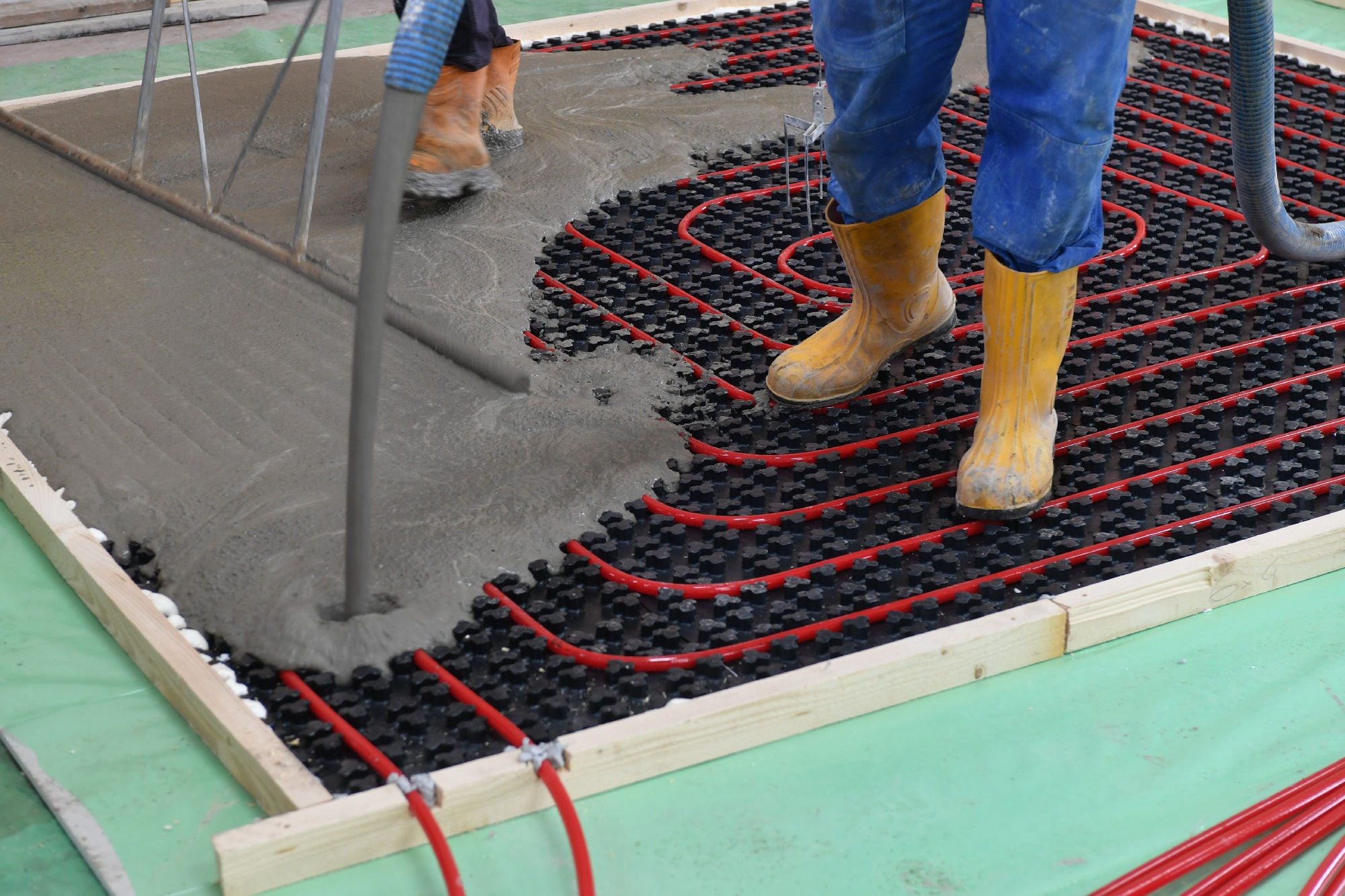
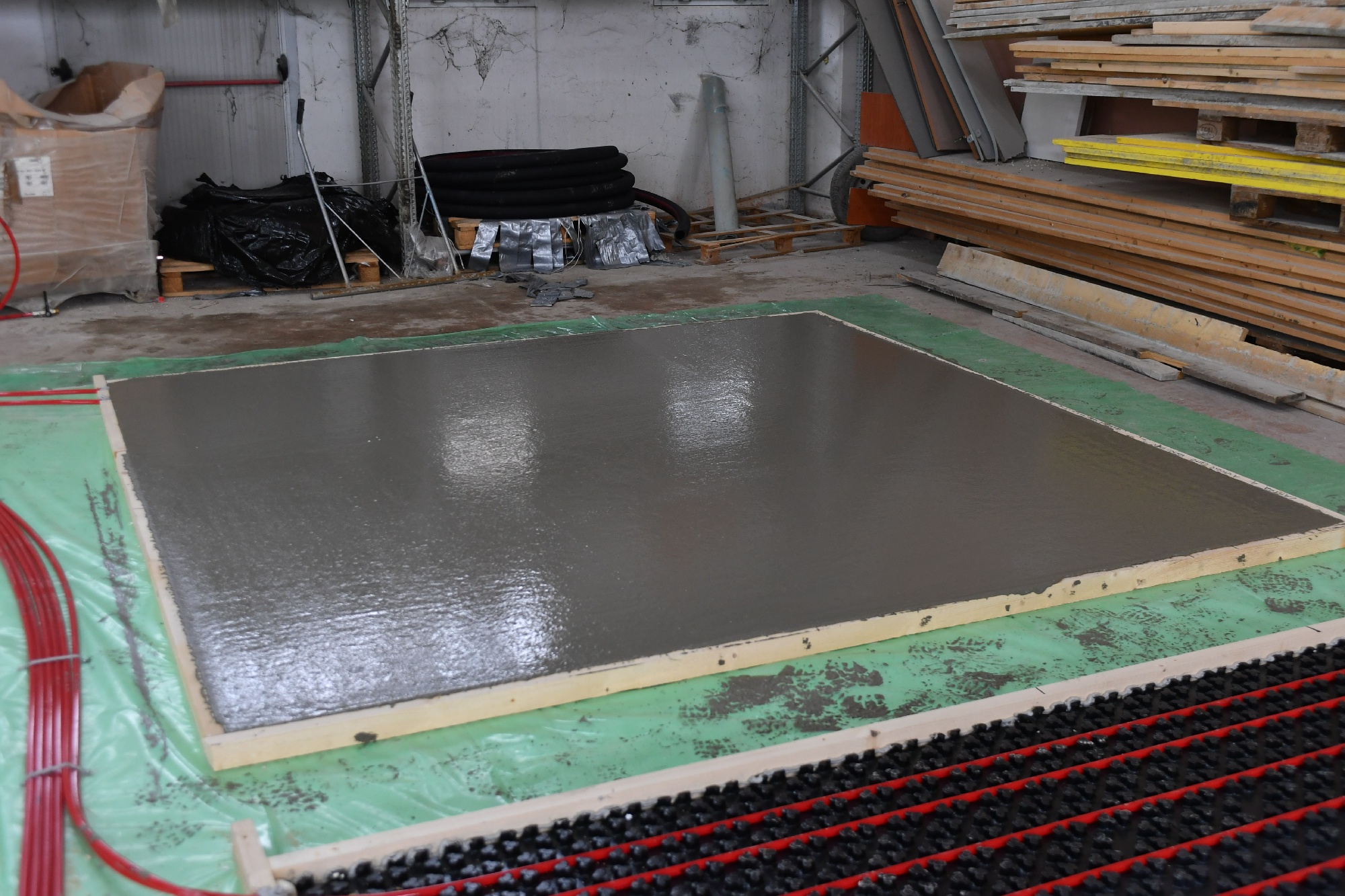
Placing and finishing 3x3 m slabs with SLS containing our innovative solution took less than half the time compared to dry screed. The significant savings in time, labor, and money are of great importance to the contractor, especially when schedules are tight.
The well-being and comfort of the workforce is another key factor in favor of the SLS technology: self-leveling screed is not only faster, but also far easier and less tiring for the workers!
*The tests were carried out with the support of the accredited lab SOCOTEC.
Superior mechanical properties, a synonym for quality and durability
![]() |
![]() |
Technology for SLS achieved a 25-50% higher compressive strength compared to alternative technologies | Flexural strength at 28 days: Technology for SLS achieved a 40% increase compared to alternative technologies |
Impact resistance and pull-off
The impact resistance, measured in both static and dynamic mode, has shown that the cement -based screeds perform significantly better compared to the anhydrite screed. In the static test (graph on the left), the higher the value, the better the result, since it indicates the height from which the weight can fall to cause the same damage to the screed. On the other hand, the dynamic test (right graph) shows the depth of damage caused by a weight falling from the same height. Thus, the lower the value, the better the performance. Anhydrite performed very poorly in both tests, while the two cementitious screeds are quite similar. |
![]() |
The pull-off (according to EN13838) is one of the most challenging requirements for screeds. The anhydrite screed achieved the worst result with values of around 1 MPa; the self-levelling cementitious screed produced with Technology for SLS significantly exceeds the value of 1.6 MPa required on average for the application of the finishing layer. |
![]() |
A convincing technology for the long-term
Dimensional stability, a reduction in shrinkage-related cracks, and an absence of curling are the most important performance criteria for screeds, as they directly influence the future stability and durability of the finished floor.
At 2 months no cracks were observed on the surface of the screeds produced with the Technology for SLS and the maximum detected deviation from planarity was a negligible 0,4mm/m.
For further information on the products and success stories of Master Builders Solutions, please visit this page.
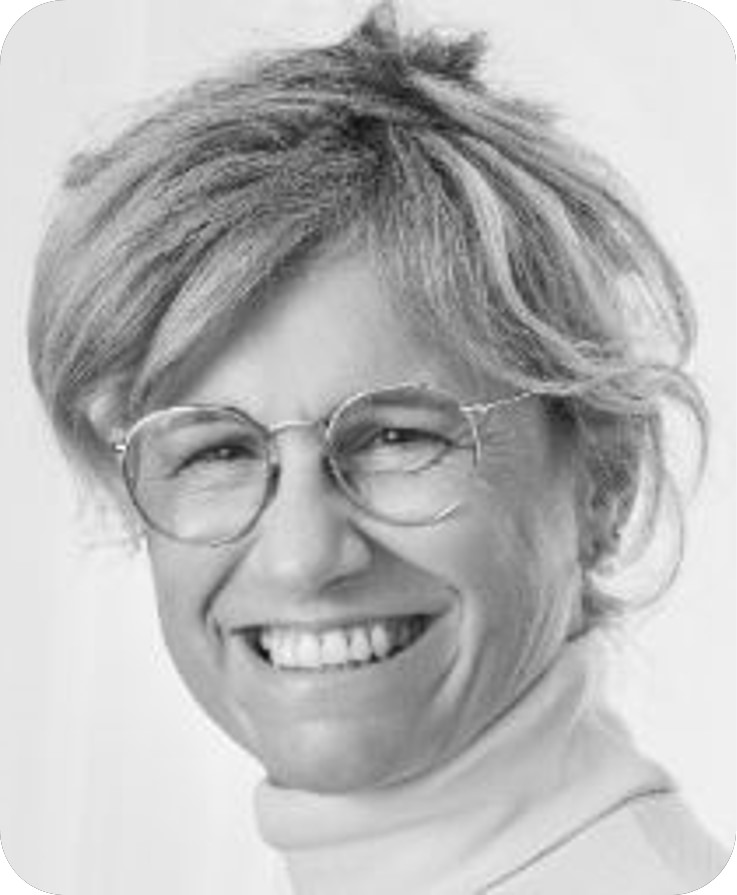
Nicoletta Zeminian