Sprayed concrete construction in double-shell lining is a CO2-intensive construction method for tunnel structures. We identify design improvement potentials and propose suggestions for ways of reducing CO2 in sprayed concrete for tunnelling applications.
Sustainability in construction
Sustainability is top of the agenda both for society and the construction sector thanks to the growing global commitment to environmental protection. Faced with the looming climate crisis and the need to make real progress towards net zero, the construction industry cannot afford to ignore the problem.
Conventional building construction is already rising to the challenge of an increasing demand for eco-friendly building materials and efficient construction methods. In material-intensive tunnel and underground construction, however, action on sustainability is lagging behind.
Access the complete article by specialists Annika Bantle, an Applied Sustainability Expert, and Dr. Wolfgang Aldrian, a Principal Expert in Tunneling, which serves as the basis for this blog post. You can download it here!
There’s a real need to catch up, as the world’s population becomes increasingly urban. By 2050, about two-thirds of us will live in cities, dependent on urban infrastructure and increasingly reliant on public transport, including new metro systems. Today, underground transport structures are usually constructed using tunnelling methods, using materials that easily adapt to changing cross-sections for the lining. So where do we go from here to achieve a more sustainable underground construction?
Plan early to reduce CO2
The key to reducing tunnels’ carbon footprint through more sustainable construction methods is to act early – which means looking at better alternatives from the planning stage onwards. Clients and designers must keep an open mind regarding design and construction options and be open to exploring construction materials that combine high quality, durability, and CO2-optimization. That might involve some myth-busting concerning the role of sprayed concrete.
Myth or fact: sprayed concrete is a temporary solution?
Sprayed concrete has many advantages, most notably ease of handling. However, despite its admirable track record for long-lasting performance, sprayed concrete’s reputation as a largely temporary support material has endured. So why isn’t permanent sprayed concrete (PSC) used on a larger scale for tunnel shells? The answer lies in a combination of concerns about durability, which can lead to over-dimensioning and thus greater concrete consumption, with a knock-on effect on a project’s carbon footprint.
Essentially, PSC has the same composition as temporary sprayed concrete – the difference being that it must be proven to last for the lifespan of the tunnel. In addition to environmental influences, the relevant factors in demonstrating durability are:
- Design
- Concrete technology
- Material parameters
- Process and application parameters
Regarding PSC mix design, a low water/binder ratio, suitable strength development and crack control for spray application are the significant factors influencing lifespan. Here, admixtures can ensure that the necessary performance characteristics are achieved. The following should be considered for PSC:
- Superplasticizer solutions for the easy application of concrete (e.g., MasterEase)
- Microsilica/Nanaosilica for improved chemical and mechanical resistance (e.g., MasterRoc MS)
- Anti-shrinkage admixtures to increase concrete durability (e.g., MasterLife SRA)
- Micro- and macrofibers for shrinkage control or structural support (e.g., MasterFiber)
The state-of-the-art technology involved in producing and applying sprayed concrete has driven significant improvements in the quality of application, too. In addition to the advantages of computerized and optimized mixing and machinery, nozzle operators are now more highly qualified. When you also consider the benefit of advances in material solutions in the cement and chemical industries, it’s no surprise that the longevity of sprayed concrete is hitting new levels.
Achievable strengths for PSC exceed the specified design strengths, and research shows that accepted structural design concepts may be much too cautious. The need for a more environmentally focused approach now puts traditional tunnel design in the spotlight for review.
Reducing the clinker factor
More than 14 billion cubic metres of concrete are used every year, making concrete today’s principal mass construction material. The environmental burden caused by concrete relates to its cement content, as producing the clinker it contains releases vast quantities of CO2 during the calcination process.
Regardless of the construction method, optimizing the concrete mix to reduce the Portland cement content should be prioritized from the planning stage onwards. Even subtle tweaks to the mix design can increase clinker efficiency and bring notable gains in the life cycle assessment of the entire structure because of the quantity of concrete involved in large scale tunnelling projects.
Challenging the status quo
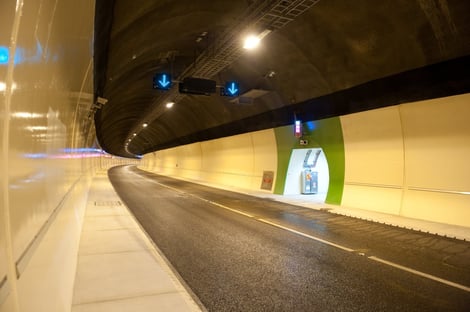
It’s fair to say that tunnelling concepts that push the design envelope are not common. This fact can be explained by a knowledge gap and the absence of relevant standards for sprayed concrete, compounded by the concerns of risk-averse planners. However, significant developments in construction materials’ quality and application by a more proficient workforce mean that stability and durability are assured.
With the option of ‘new and improved’ sprayed concrete linings as a genuine choice, there is a strong argument for allowing aesthetic demands and tunnel usage requirements to guide construction methods. Many sections of a tunnel’s network, such as service tunnels, are less visible, and here a sprayed-concrete surface may be entirely acceptable.
Comparing the CO2 balance of a metre-long tunnel section using PSC to a traditional double-shell lining of temporary sprayed concrete and a permanent inner shell, the PSC performs best, thanks to using much less concrete.
Three tactics to reduce CO2 emissions with sprayed concrete
Sprayed concrete is the natural choice of support material and, as such, it can’t be eliminated from a tunnel’s design when applying the New Austrian Tunneling Method (NATM) to reduce concrete usage. However, optimizing the amount of concrete used through design changes without compromising structural integrity is viable at the planning stage, depending on the feasibility for the project. Here are three possible options:
- Designate all/part of the sprayed concrete as a permanent lining, included in the structural design.
- Use a sprayed inner shell if appropriate and if a minimum thickness of conventionally constructed inner shell is required purely for constructability reasons
- Connect the inner and outer shells if feasible and practical
Employing one of these tactics can significantly reduce the CO2 footprint of a tunnel structure built using sprayed concrete – approximately by 10-30 % [1, 2], depending on the static loading assumptions and concrete mix designs. Whichever methods you explore, it’s essential to understand how much excess thickness and higher concrete strength can be factored into static loading calculations and to what degree an additional inner lining is required.
With stretching environmental targets to meet, the pressure to use more sustainable approaches is a priority. It must be treated as a key metric, not only during planning but at the tendering stage. Both conventional methods and ecologically optimized approaches must be considered for every project.
Access the complete article by specialists Annika Bantle, an Applied Sustainability Expert, and Dr. Wolfgang Aldrian, a Principal Expert in Tunneling, which serves as the basis for this blog post. You can download it here!
References:
[1] Permanent Sprayed Concrete Linings; Aldrian W., Thomas A., Chittenden N., Holter K.G.; ITA Working Group n°12 and ITAtech AG Lining, Support & Waterproofing, Lausanne 2020
[2] Composite tunnel linings, allowing a more cost effective and sustainable tunnel design; Jung H., Clement F., Pillai A., Wilson C., Traldi D.; World Tunnel Congress 2017 Bergen
/in%20USE/Wolfgang%20Aldrian-2.png)
Wolfgang Aldrian