Segmentally lined tunnels use a large quantity of concrete, with the associated carbon burden that brings. However, rethinking your approach early on can reduce the carbon footprint they leave. We take a look at 10 ways you can reduce segmental tunnel linings’ carbon footprint...
1. Reduce the amount of cement used in tunnel construction
Cutting down on the amount of cement you used can make a massive difference. In fact, with as much as two-thirds of carbon emissions resulting from cement usage, it’s probably the single most important measure you can take. Strength boosting admixtures such as Master X-Seed permit a reduction in the total cementitious materials content while maintaining compressive strength with associated benefits in CO2 reduction.
Addressing the issue early on is key – which means thinking about carbon emissions at the design stage. Consider the aspects of your design that could make the most difference to lowering the CO2 emissions, including:
- Tunnel alignments
- Structural support
- Excavation methods
- Material selection
Making decisions too late on any of these aspects reduces the potential to cut carbon significantly.
2. Include life cycle assessments (LCAs) at the design stage
Life cycle assessments (LCAs) calculate the potential environmental impacts of a product system throughout its life cycle. ISO 21930 Sustainability in buildings and civil engineering works specifies four life cycle stages:
- Production (A1-A3)
- Construction (A4-A5)
- Use (B1-B7)
- End-of-life (C1-C4)
For tunneling projects, it’s essential to add the design phase to these LCA stages. Even though no relevant emissions result from the design process itself, its influence on later emissions is highly relevant.
3. Consider the implications of early design decisions carefully
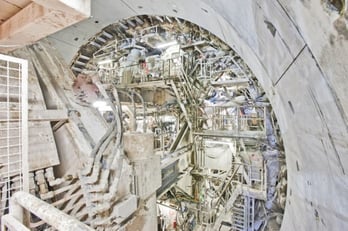
Early design decisions can make a big difference to CO2 reduction. Thinks about the following as you assess the environmental implications:
- What are the alignment variations?
- Will you opt for twin tunnels or one large tunnel?
- Do you plan to excavate with a TBM rather than NATM?
- Will you choose a single shell, double shell or composite lining?
The decisions you make will determine how much concrete the project will use and its quality, and dictate the mix designs needed to fulfil your engineering and placement requirements.
4. Understand the impact of the construction phase
In any tunneling project, greenhouse gas (GHG) emissions are very high during construction, firstly because of materials’ manufacture and secondly because of the construction activity itself.
Beyond initial construction, the need for future maintenance, and the likely scale of remedial works during the use phase, are dictated by the skills of the workforce and material selection during construction. The knock-on effect on later CO2 emissions can be significant – less durable construction leads to more emissions due to more frequent and material-intensive maintenance needs.
5. Think about transportation
The choice of transportation modes and distances for raw materials can have a significant effect, too, so you should analyze this separately for each project.
In practice, owners should incorporate sustainability targets and carbon budgets when putting contracts out to tender, and these elements should form part of the contract documents. Stating a clear commitment to sustainability paves the way for innovative, sustainable tunnel construction that factors in reduced use-phase maintenance and repair – and hence emissions – thanks to more durable, resilient designs. Currently, the purely capital cost-driven approach to construction only addresses emissions reductions as an afterthought.
6. Compare design options from a CO2 reduction perspective
When weighing up the design options, take CO2 emissions into account as you make a decision. For example, one larger-diameter tunnel appears to be better than two smaller twin tunnels for carbon emissions, purely from a structural support perspective. Here, the large tunnel might be the better option when the free space is fully used, although two smaller tunnels could be preferred for safety reasons when traffic is involved.
7. Optimize your concrete mix design
Once you have settled all of the fundamental design decisions, you can optimize the concrete mix design to improve sustainability and achieve significant carbon reductions. For segmental tunnels, optimizing mix design can lead to a 20 % reduction in the carbon footprint of materials for the lining, or around 15 % of the total project footprint.
The key factors here are the total amount of cement and the cement type. As you weigh up the options, consider the need for 28-day concrete strength versus 56-day testing, if the full load-bearing capacity might not be required at a young concrete age. If higher early concrete strength is essential to allow the handling and bedding of prefabricated segments, assess whether concrete admixtures like Master X-Seed could be used to boost strength, adding less total carbon to the mixture than increased cement content.
Different types of cement give varying levels of embodied carbon, so another consideration is increasing the cement strength class. While this can increase carbon emissions per kilogram of cement, it reduces the overall cement amount in the mixture. Reduced clinker content significantly lowers the global warming potential of the cement. Achievable reductions will be affected by regional variations in raw materials, energy sources and production processes.
8. Look at the reinforcement and curing
Looking beyond the mix design, the choice of reinforcement and the curing method for the segments may also contribute to the carbon burden. Steel bar reinforcement, for example, is heavy, difficult to handle, and prone to corrosion but sometimes unavoidable. Structural fibers can partially or completely replace the steel bar reinforcement. Mixed into the fresh concrete, the fibers (e.g. MasterFiber) form an internal network and add superior tensile properties to the concrete elements. The result is improved crack control and stronger concrete, which in turn leads to less maintenance work and overall longer service life of the tunnel structure.
9. Don’t overlook the CO2 contribution of annulus grouting
The annulus grout fills the overcut of the cutter head around the segments, stabilizing them and allowing the load from the ground to transfer homogeneously onto the segments. It’s a significant carbon contributor in tunnel construction materials, and, crucially, there is a big difference between the broader environmental impact of different types of grout.
Two-component grouting systems are increasingly widely used, mainly because of ease of application; they comprise a cement-water-bentonite component and a water glass (sodium silicate) component for gelling and strength gain. The environmental concerns involve the high pH level of the water glass, potential leaching effects, durability concerns, and the need for increased cement content.
The biggest reduction in carbon relating to the grout comes from switching from a two-component system to a single-component grout with lower cement content where possible. However, future-oriented innovation opportunities that meet owners' expectations for quality, durability, and carbon footprint may lay somewhere between the two solutions mentioned above.
10. Encourage innovative approaches
As you seek to balance out the needs for quality, durability, and CO2 reduction, keep an open mind to new technical solutions that meet expectations while meeting constructability requirements for the contractor. Even using traditional techniques and technology, it is entirely possible to reduce tunneling projects’ carbon footprint. The CO2 eq burden should become an integral part of the decision process, helping to inform the earliest decisions about a tunnel’s route and construction.
Want to find out more? Download Wolfgang Aldrian’s full article "Reducing the carbon footprint of segmental linings", on which this blog is based here.
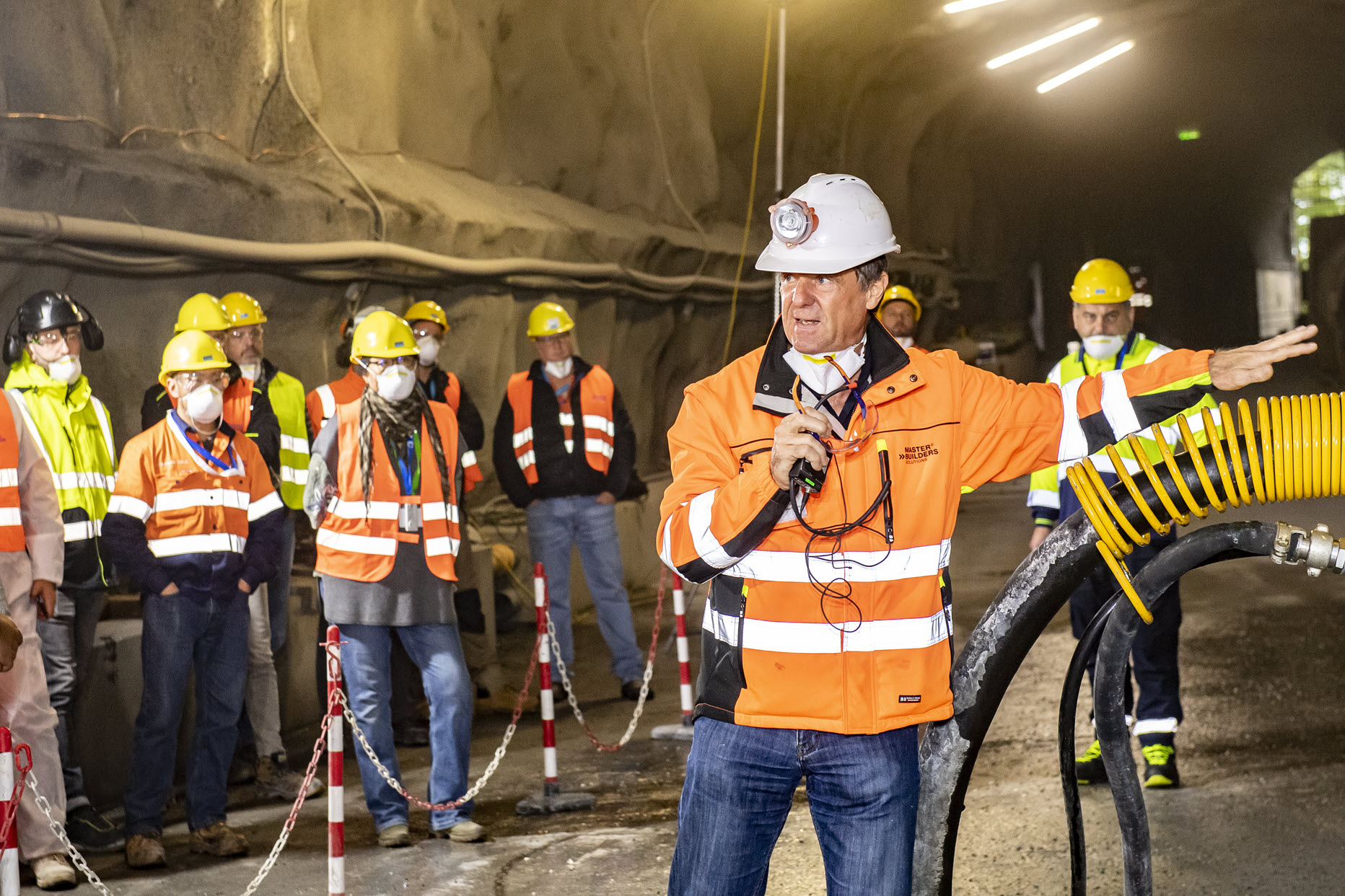
Wolfgang Aldrian